When your furnace struggles to ignite, you might see codes like “1-4” for ignition lockouts. This could be due to a dirty flame sensor or a faulty igniter.
Now that we’ve covered the basics, let’s break down those error codes into categories for better clarity.
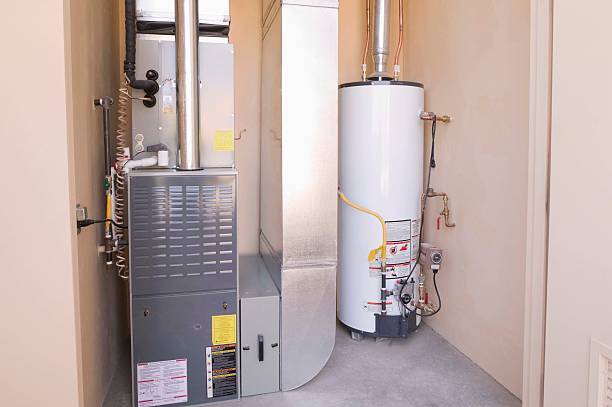
Table of Contents
If your Bryant furnace suddenly stops working and starts blinking mysterious lights at you, don’t panic. These error codes are your furnace’s way of telling you exactly what’s wrong. Instead of guessing, you can decode the issue and, in some cases, even fix it yourself. In this guide, we’ll break down what the bryant Furnace error code means, how serious it is, and what you can do to get your furnace up and running again.
About Bryant – Reliable and Innovative
Bryant has been in the HVAC industry for over a century, building a reputation for reliability, efficiency, and innovation. Founded in 1904, the company has continuously evolved, offering some of the most energy-efficient and durable furnaces on the market today.
So, why Choose a Bryant Furnace?
- Energy Efficiency: Many Bryant models feature high AFUE ratings, meaning they convert a significant portion of fuel into usable heat, saving you money on energy bills.
- Durability: With proper maintenance, a Bryant furnace can last 15-20 years, outperforming many competitors.
- Smart Technology: Modern models are equipped with smart diagnostics and compatibility with home automation systems for easy monitoring.
- Reliable Performance: These furnaces are designed to withstand harsh Canadian winters, ensuring consistent heating.
How Reliable Are Bryant Furnaces?
Bryant furnaces are widely recognized for their reliability, but like any appliance, they’re not immune to occasional issues.
Average Lifespan
Each flash code is a signal that can help pinpoint specific issues with your system. Understanding what each color and pattern means can help you troubleshoot and possibly fix the problem before it gets worse.
Common Issues vs. Other Brands
Compared to competitors like Lennox and Trane, Bryant furnaces have a similar failure rate. However, users report fewer issues with major components like heat exchangers and gas valves.
Most Frequent Problems
- Ignition Failure – Often due to a dirty flame sensor or faulty ignitor.
- Airflow Blockage – This common furnace issue is caused by clogged filters or blower motor failure.
- Flame Sensor Malfunction – Can result in the furnace shutting down unexpectedly.
Bryant Furnace Error Codes and Solutions
Here’s a detailed breakdown of the most common Bryant furnace error codes, what they mean, and how to fix them.
Code 11: No Previous Error Code
Explanation | Stored status codes are automatically erased after 72 hours or per specific system settings. |
---|---|
Solution
| No action is required. |
Code 12: Blower Running After Power Up (115V AC or 24V AC)
Description | The blower runs for 90 seconds if the unit is powered on during a heating call (R-W/W1 contacts closed) or if the R-W/W1 contacts open during a fan-off delay. |
---|---|
Explanation | No fix is needed unless the blower continues running indefinitely, in which case a control board issue may be present.
|
Code 13: Limit Circuit Lockout
Description | Lockout occurs if the limit switch or flame rollout switch remains open for over 3 minutes or if there are 10 consecutive high-heat limit trips. |
---|---|
Explanation | Check airflow, clean filters, and ensure the blower is operating correctly.
|
Code 14: Ignition Lockout
Explanation | The controller will automatically reset after 3 hours. |
---|---|
Solution | Inspect the ignitor, gas valve, and flame sensor for issues. |
Code 21: Gas Heating Lockout
Explanation | The controller does not automatically reset after 3 hours. |
---|---|
Solution | A professional technician should inspect the system.
|
Code 22: Abnormal Flame-Proving Signal
Explanation | Flame is detected when the gas valve is not active. The inducer will run until the fault is cleared. |
---|---|
Possible Causes
| Leaking or stuck-open gas valve.
|
Solution
| Inspect and replace the gas valve if necessary. |
Code 23: Pressure Switch Did Not Open
Explanation | The pressure switch is stuck closed when it should be open. |
---|---|
Possible Causes | Blocked pressure tubing, stuck pressure switch.
|
Solution
| Clear the tubing and check the switch for defects.
|
Code 24: Secondary Voltage Fuse Open
Explanation | Short circuit in the 24V secondary voltage wiring. |
---|---|
Solution
| Inspect for faulty wiring and replace the fuse if necessary.
|
Code 31: High-Stage Pressure Switch or HPSR Failure
Explanation | The high-pressure switch input did not close when high heat was requested or opened during high heat operation. |
---|---|
Solution
| Inspect the HPSR relay and pressure switch. |
Code 32: Low-Stage Pressure Switch Failure
Explanation | The low-pressure switch input did not close when low heat was requested or opened during low heat operation. |
---|---|
Possible Causes | Incorrect vent size, improper wiring, combustion air restriction, condensate drainage issue, excessive wind, low gas pressure, blocked pressure tubing, water in the vent pipe.
|
Solution
| Inspect and correct the issue based on the specific cause.
|
Code 33: Limit Circuit Fault
Explanation | The limit switch or flame rollout switch has opened, or the furnace is running in high heat mode due to two consecutive limit trips on low heat. |
---|---|
Solution
| Check limit switch calibration, fan wheel condition, and gas valve solenoid operation. |
Code 34: Ignition-Proving Failure
Each of these Bryant furnace codes gives you insight into what’s happening with your HVAC unit. Some can be fixed easily, while others require a professional. If you’re dealing with repeated shutdowns or safety-related errors, calling a professional furnace repair service is the best move.
Explanation | The controller will make three more attempts before going into lockout (Code 14). |
---|---|
Possible Causes | Dirty flame sensor, closed manual gas valve, grounding issues.
|
Solution
| Clean the flame sensor, check the gas valve, and ensure proper grounding.
|
How Often Do Bryant Furnaces Break Down?
Bryant furnaces are known for their reliability, but like any mechanical system, certain components can wear out over time. Commonly replaced parts include the flame sensor, which may need cleaning or replacement every 3-5 years, the inducer motor, which can fail after 10-15 years, the blower motor, which can wear out from dust buildup or electrical issues, and the pressure switch, which is susceptible to failure due to moisture accumulation.
Bryant furnace owners who keep up with regular maintenance generally report fewer breakdowns. However, neglecting annual tune-ups increases the likelihood of issues, especially with sensors and airflow components. Regular furnace maintenance helps to ensure smooth operation and extend the lifespan of your furnace.
How Much Does Repair a Bryant Furnace in Canada Cost?
The cost of repairing a Bryant furnace can vary depending on what’s broken and how serious the issue is. Some parts are more expensive to fix than others, and it’s important to weigh the cost of repair against the cost of replacement. Below are estimated repair costs for some of the most common issues:
Component | Estimated Repair Cost (CAD) |
---|---|
Flame Sensor | $100 – $300 |
Ignitor Replacement
| $150 – $350 |
Gas Valve
| $400 – $700 |
Blower Motor
| $500 – $900 |
Heat Exchanger
| $1,500 – $3,000 |
For some components, like the heat exchanger, repairs can get pretty expensive. If the cost of fixing your furnace is more than 50% of the price of a new one, it might be more economical to just replace the entire unit. Other factors to consider are the age of your furnace—if it’s already several years old, you might end up facing more issues down the road. Also, check if your furnace is still under warranty, as it could cover some of these costs. In many cases, replacing an old furnace with a newer, more energy-efficient model could save you money in the long run, both on repairs and energy bills.
Check out our previous article to find out how you can save up to $ 10,000 on your new furnace with government rebates in Ontario.
When to Call a Professional Bryant Furnace Repair?
While some minor Bryant furnace issues, like checking or replacing air filters, resetting the furnace, or cleaning the flame sensor, can be handled by homeowners, more complex situations require a professional. If your furnace frequently shuts down, you notice a gas smell or carbon monoxide alerts, or if there are electrical faults or control board failures, it’s essential to call a certified technician. These problems can be dangerous and require specialized knowledge to diagnose and repair safely.
For peace of mind and expert service, reach out to HVAC Service Solutions. Our licensed technicians are ready to address any Bryant furnace error code or issue, ensuring your furnace operates safely and reliably.
FAQs
1. What does it mean if my Bryant furnace is flashing an error code?
When your Bryant furnace flashes an error code, it indicates that the system has detected an issue that needs attention. Each error code corresponds to a specific malfunction in the system. For example, a Code 13 (Limit Circuit Lockout) could mean there’s a problem with airflow or a dirty filter, while a Code 22 (Abnormal Flame-Proving Signal) could suggest an issue with the gas valve. By referring to your furnace’s manual or using the error code, you can understand what might be causing the problem. Some codes, like Code 11 (No Previous Error Code), don’t require action, while others may need troubleshooting or professional repair.
2. How can I reset my Bryant furnace after an error code appears?
In most cases, a simple reset can clear minor issues, but the process depends on the specific error code. For instance, if your furnace displays a Code 14 (Ignition Lockout), the system will automatically reset after 3 hours. For other codes, you can try turning off the power to the furnace for 5 minutes and then turning it back on. If the code persists after resetting or if the system continues to malfunction, it’s best to call a professional HVAC technician to address the underlying issue, such as a faulty flame sensor or gas valve.
3. What are the most common Bryant furnace error codes?
Common error codes include Code 13 (Limit Circuit Lockout), which is typically caused by airflow issues or dirty filters, and Code 22 (Abnormal Flame-Proving Signal), often due to a leaking or stuck-open gas valve. Other codes, like Code 23 (Pressure Switch Did Not Open), may point to a blocked pressure switch or tubing, while Code 34 (Ignition-Proving Failure) could indicate a dirty flame sensor. Each error code offers a clue to what’s malfunctioning, and addressing the specific cause will help restore your furnace to normal operation.
4. Why does my Bryant furnace flash an error code after a power surge?
Power surges can cause electrical components in your Bryant furnace to malfunction, leading to error codes like Code 24 (Secondary Voltage Fuse Open). A surge may cause short circuits in the 24V secondary wiring, triggering a fuse to blow. In such cases, check the wiring and replace the fuse if necessary. If the error code persists, it could indicate more serious damage, such as a faulty control board, requiring a professional technician to assess and repair.
5. How can I troubleshoot a Bryant furnace flashing an error code for the flame sensor?
If your furnace is flashing Code 34 (Ignition-Proving Failure), it may be due to a dirty flame sensor. To troubleshoot, turn off the furnace power and clean the flame sensor using a soft cloth or fine sandpaper. If cleaning doesn’t resolve the issue, check for grounding issues or a closed manual gas valve. If the problem persists, the flame sensor may need to be replaced. However, if you’re not comfortable performing these steps, it’s safer to call a technician to avoid causing further issues.
6. Is it safe to continue using my Bryant furnace with an error code?
It’s not recommended to continue using your Bryant furnace if it’s displaying an error code, especially if the issue involves safety components. For instance, Codes 21 (Gas Heating Lockout) and 22 (Abnormal Flame-Proving Signal) point to issues with the gas valve, which could pose a fire hazard if not addressed. If the system is displaying any of these codes, it’s best to turn off the furnace and contact a professional HVAC technician to inspect and repair the system.
7. Can I fix a Bryant furnace flashing an error code myself?
Some minor issues, such as cleaning the flame sensor or checking filters, can be handled by homeowners, but many error codes indicate more complex issues that require a professional’s expertise. For example, Code 23 (Pressure Switch Did Not Open) may require clearing blocked tubing or inspecting the switch for defects, while Code 32 (Low-Stage Pressure Switch Failure) could involve more technical troubleshooting. If you’re unsure of the cause or the issue persists, it’s always best to contact a certified HVAC technician to avoid causing further damage.
8. What does it mean if my Bryant furnace is flashing a 4-flash error code?
The 4-flash error code indicates an issue with the limit circuit, such as a tripped limit switch or an open flame rollout switch. It can also occur if the furnace is running in high heat mode due to consecutive trips on low heat. To resolve this, check the limit switch calibration, inspect the fan wheel, and ensure the gas valve solenoid is working correctly. If these steps don’t solve the issue, you may need to replace the limit switch or other components, so contacting a professional is recommended.
9. What should I do if my Bryant furnace is flashing a 2-flash error code?
A 2-flash error code typically points to an abnormal flame-proving signal, which often means the flame is detected when the gas valve is not active. This could be caused by a leaking or stuck-open gas valve. To fix this, inspect the gas valve for any signs of damage or malfunction and replace it if necessary. If the issue persists after checking the valve, it’s best to call a professional to ensure the furnace is safe to operate.
10. How do I know when it’s time to call a professional for furnace repairs?
If your Bryant furnace is flashing an error code and you’ve already tried basic troubleshooting like resetting or cleaning the flame sensor, but the issue remains unresolved, it’s time to call a professional. Codes like 21 (Gas Heating Lockout) or 31 (High-Stage Pressure Switch Failure) often require specialized knowledge and tools to diagnose and repair. HVAC Service Solutions offers expert repairs to ensure your furnace is functioning safely and efficiently, addressing any error codes and restoring comfort to your home.
Share