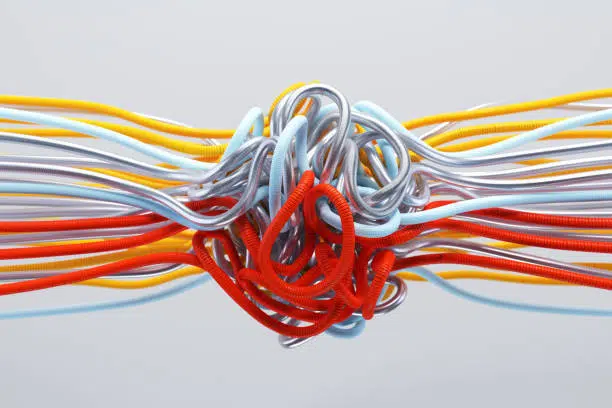
Table of Contents
A furnace is one of the most essential components of any home’s HVAC system, especially in Canada’s harsh winters. However, like any mechanical system, furnaces can develop issues over time. When your Arcoaire furnace encounters a problem, it displays error codes through a series of LED flashes to help diagnose the issue. Understanding these Arcoaire furnace error codes is crucial for homeowners and HVAC professionals alike, as they provide valuable insights into what’s wrong and how to fix it.
In this guide, we’ll break down the most common Arcoaire furnace error codes, their meanings, and possible solutions. We’ll also provide insights into why furnaces fail, how Arcoaire stands out as a brand, and when it’s best to call a professional HVAC technician.
About the Arcoaire Brand
Arcoaire is a well-known name in the HVAC industry, recognized for its reliability and efficiency. Manufactured under the umbrella of International Comfort Products (ICP), a subsidiary of Carrier Global Corporation, Arcoaire offers high-performance heating and cooling solutions designed for both residential and commercial use.
Arcoaire furnaces in Canade are built with advanced technology, including variable-speed blowers, modulating gas valves, and smart diagnostics that help homeowners troubleshoot issues efficiently. Their systems are known for energy efficiency, with many models boasting AFUE ratings of 96% or higher, ensuring maximum heat output with minimal fuel consumption.
Despite their high-quality construction and durability, Arcoaire furnaces can still experience problems due to wear and tear, lack of maintenance, or faulty components. Understanding the brand’s Arcoaire furnace error codes system is crucial for ensuring optimal furnace performance and avoiding costly repairs.
Common Causes of Furnace Issues
Before diving into specific Arcoaire furnace error codes, it’s helpful to understand the common reasons why a furnace might fail. Recognizing these issues can help prevent breakdowns and extend the lifespan of your Arcoaire furnace.
- Dirty or Clogged Air Filters – A blocked air filter restricts airflow, forcing the furnace to work harder. This can lead to overheating, short cycling, and even system shutdowns.
- Ignition System Failures – Issues with the ignitor, flame sensor, or gas supply can prevent the furnace from lighting, resulting in repeated startup failures.
- Faulty Pressure Switches – The pressure switch ensures proper airflow before ignition. A malfunctioning switch may prevent the furnace from operating safely.
- Blocked Venting or Flue Pipes – If exhaust gases cannot escape properly, the furnace will shut down as a safety precaution.
- Blower Motor Malfunctions – A faulty blower can cause inadequate heating, overheating, or prevent warm air from being distributed effectively.
- Electrical Issues – Problems with wiring, circuit breakers, or control boards can disrupt furnace operation.
Understanding these issues can make it easier to diagnose and fix furnace problems before they escalate.
How Arcoaire Furnace Error Codes Work
Arcoaire furnaces use an LED flashing system to indicate error codes. These flashes appear on the control board inside the furnace panel. Each pattern of flashes corresponds to a specific issue, making it easier to diagnose problems quickly.
To read an error code:
- Locate the LED light on your furnace control board.
- Count the number of flashes before and after a pause.
- Refer to the furnace’s manual or the chart below to determine the problem.
Arcoaire Furnace Error Codes and Fixes
Below, we’ve prepared the list of the most frequent Arcoaire furnace error codes, their explanations, possible reasons for the malfunction, and steps to fix them.
Error Code 1 Flash – Ignition Failure
- Cause: The furnace tried to ignite three times but failed.
- Solution: Check for gas supply issues, a dirty flame sensor, or a faulty ignitor. Cleaning or replacing these components may resolve the issue.
Error Code 2 Flashes – Pressure Switch Stuck Open
- Cause: The pressure switch is not closing when it should, preventing the furnace from operating.
- Solution: Inspect venting for blockages, ensure the inducer motor is functioning, and check pressure switch tubing for leaks.
Error Code 3 Flashes – Pressure Switch Stuck Closed
- Cause: The switch is not opening when required, possibly due to electrical faults or condensation buildup.
- Solution: Check for clogged condensate drains, a defective pressure switch, or a control board malfunction.
Error Code 4 Flashes – High Limit Switch Open
- Cause: The furnace is overheating due to restricted airflow.
- Solution: Replace or clean the air filter, check for blocked vents, and ensure proper blower motor operation.
Error Code 5 Flashes – Rollout Switch Tripped
- Cause: Excessive heat buildup near the burners, possibly due to a cracked heat exchanger or blocked exhaust vent.
- Solution: Reset the rollout switch if safe, inspect the heat exchanger for cracks, and clear vent obstructions.
Error Code 6 Flashes – Faulty Inducer Motor
- Cause: The inducer motor is not starting or running properly.
- Solution: Ensure the motor receives power, check wiring connections, and replace the motor if necessary.
Error Code 7 Flashes – Faulty Gas Valve
- Cause: The gas valve is not opening properly.
- Solution: Inspect the gas line for blockages, check the gas pressure, and replace the valve if necessary.
Error Code 8 Flashes – Internal Control Board Failure
- Cause: The control board has failed due to electrical issues or component failure.
- Solution: Reset the furnace, check wiring connections, and replace the control board if needed.
Error Code | Explanation | Solution |
---|---|---|
1 Flash
| Ignition Failure
| Check gas supply, clean or replace flame sensor, ignitor |
2 Flashes
| Pressure Switch Stuck Open
| Inspect venting, check inducer motor, examine pressure switch tubing |
3 Flashes
| Pressure Switch Stuck Closed
| Check condensate drains, pressure switch, control board |
4 Flashes
| High Limit Switch Open
| Replace air filter, check vents, inspect blower motor |
5 Flashes
| Rollout Switch Tripped
| Reset switch, check heat exchanger, clear exhaust vent |
6 Flashes
| Faulty Inducer Motor
| Check power, inspect wiring, replace motor if needed |
7 Flashes
| Faulty Gas Valve
| Inspect gas line, check gas pressure, replace valve |
8 Flashes
| Internal Control Board Failure
| Reset furnace, check wiring, replace control board |
DIY Fixes vs. When to Call a Professional
While some furnace problems can be fixed with basic troubleshooting, others require the expertise of a licensed HVAC technician. Simple DIY fixes include changing air filters, checking power connections, resetting the furnace, and inspecting vents for blockages. However, if the issue involves gas valves, control boards, or persistent ignition failures, professional repair is necessary to avoid safety hazards.
Preventative Maintenance for Your Arcoaire Furnace
Keeping your Arcoaire furnace in top condition requires regular furnace maintenance. Here are seven essential maintenance tips:
- Change Air Filters Monthly – A clean filter improves airflow and efficiency.
- Schedule Annual Inspections – Professional check-ups catch potential problems early.
- Keep Vents and Ducts Clean – Ensure unobstructed airflow throughout your home.
- Check and Clean the Flame Sensor – A dirty sensor can cause ignition issues.
- Inspect Exhaust and Intake Pipes – Blockages can lead to improper combustion and system shutdowns.
- Test the Thermostat Regularly – Ensure it responds correctly to temperature changes.
Lubricate Moving Parts – Reduce wear and tear on motors and fans for optimal performance.
Conclusion
If you’re experiencing furnace issues and need expert help, contact our HVAC Service Solutions Company in Canada. Our experienced technicians can diagnose, repair, and maintain your Arcoaire furnace, ensuring your home stays warm and comfortable throughout the winter.
FAQs
1. What does the "Ignition Failure" (1 Flash) error mean on my Arcoaire furnace?
The “Ignition Failure” error occurs when the furnace attempts to ignite three times but fails. This is often caused by a gas supply issue, a dirty flame sensor, or a faulty igniter. To fix it, first, check the gas supply to ensure there is no interruption. Then, clean the flame sensor and inspect the igniter. If they appear damaged or malfunctioning, they may need to be replaced to restore proper ignition.
2. How do I fix the "Pressure Switch Stuck Open" (2 Flashes) error?
The “Pressure Switch Stuck Open” error indicates that the pressure switch is not closing properly, which can prevent the furnace from running. To resolve this issue, inspect the venting system for blockages, check the inducer motor to make sure it’s functioning correctly, and examine the pressure switch tubing for any leaks. If the switch or tubing is damaged, replacing them may fix the problem and restore furnace function.
3. What should I do if I get the "High Limit Switch Open" (4 Flashes) error?
This error suggests that the furnace is overheating due to restricted airflow. To resolve it, start by checking and replacing the air filter if it’s clogged, as this can significantly reduce airflow. Also, make sure the vents are clear of any obstructions, and inspect the blower motor to ensure it’s working correctly. If the motor is malfunctioning, it may need to be repaired or replaced.
4. How can I fix the "Rollout Switch Tripped" (5 Flashes) error?
The “Rollout Switch Tripped” error is typically caused by excessive heat buildup near the burners, possibly due to a blocked exhaust vent or a cracked heat exchanger. To fix this, first, reset the rollout switch if it’s safe to do so. Then, inspect the heat exchanger for any cracks or damage, as this can lead to dangerous heat buildup. If the exhaust vent is blocked, clear it to allow proper ventilation and prevent overheating.
5. What do I do if I get the "Faulty Inducer Motor" (6 Flashes) error?
This error indicates that the inducer motor is not operating properly. Start by ensuring the motor is receiving power, and check all wiring connections to ensure there are no loose or damaged wires. If the motor is still not working, you may need to replace it. A faulty inducer motor can lead to improper airflow and prevent the furnace from operating, so it’s crucial to address this issue promptly.
6. How do I fix the "Gas Valve Failure" (7 Flashes) error?
A “Gas Valve Failure” occurs when the gas valve fails to open properly. To address this issue, first inspect the gas line for any blockages or restrictions that could be preventing the flow of gas. Additionally, check the gas pressure to ensure it is within the proper range. If everything looks fine and the valve is still not functioning, it may need to be replaced to restore proper furnace operation.
7. When should I call a professional to repair my furnace?
While some furnace issues can be resolved with DIY fixes, problems with the gas valve, control board, or repeated ignition failures require professional expertise. A licensed HVAC technician has the necessary training and tools to safely diagnose and repair these complex issues. It’s crucial to call a professional when dealing with gas components or electrical failures to avoid safety hazards and ensure a proper fix.
8. What does the "Pressure Switch Stuck Closed" (3 Flashes) error mean?
The “Pressure Switch Stuck Closed” error means that the pressure switch is not opening as it should, which can be caused by a clogged condensate drain, a faulty pressure switch, or a control board malfunction. To resolve this, start by checking the condensate drains for blockages and ensuring that water can flow freely. If the problem persists, the pressure switch or the control board may need to be inspected or replaced to restore proper operation.
9. What should I do if I get the "Internal Control Board Failure" (8 Flashes) error?
The “Internal Control Board Failure” error suggests that the furnace’s control board is malfunctioning due to electrical issues or component failure. First, try resetting the furnace to see if the error clears. If the issue persists, check the wiring connections to ensure they are secure. In many cases, a faulty control board needs to be replaced to restore the furnace’s functionality.
10. How can I prevent errors on my Arcoaire furnace?
Regular maintenance is key to preventing many furnace errors. Be sure to replace or clean air filters monthly to maintain proper airflow. Additionally, schedule annual inspections to catch potential issues early. Cleaning the flame sensor, checking for blockages in the exhaust and intake pipes, and testing the thermostat regularly can also help keep your furnace running smoothly. By staying on top of these maintenance tasks, you can reduce the likelihood of experiencing error codes.
Share